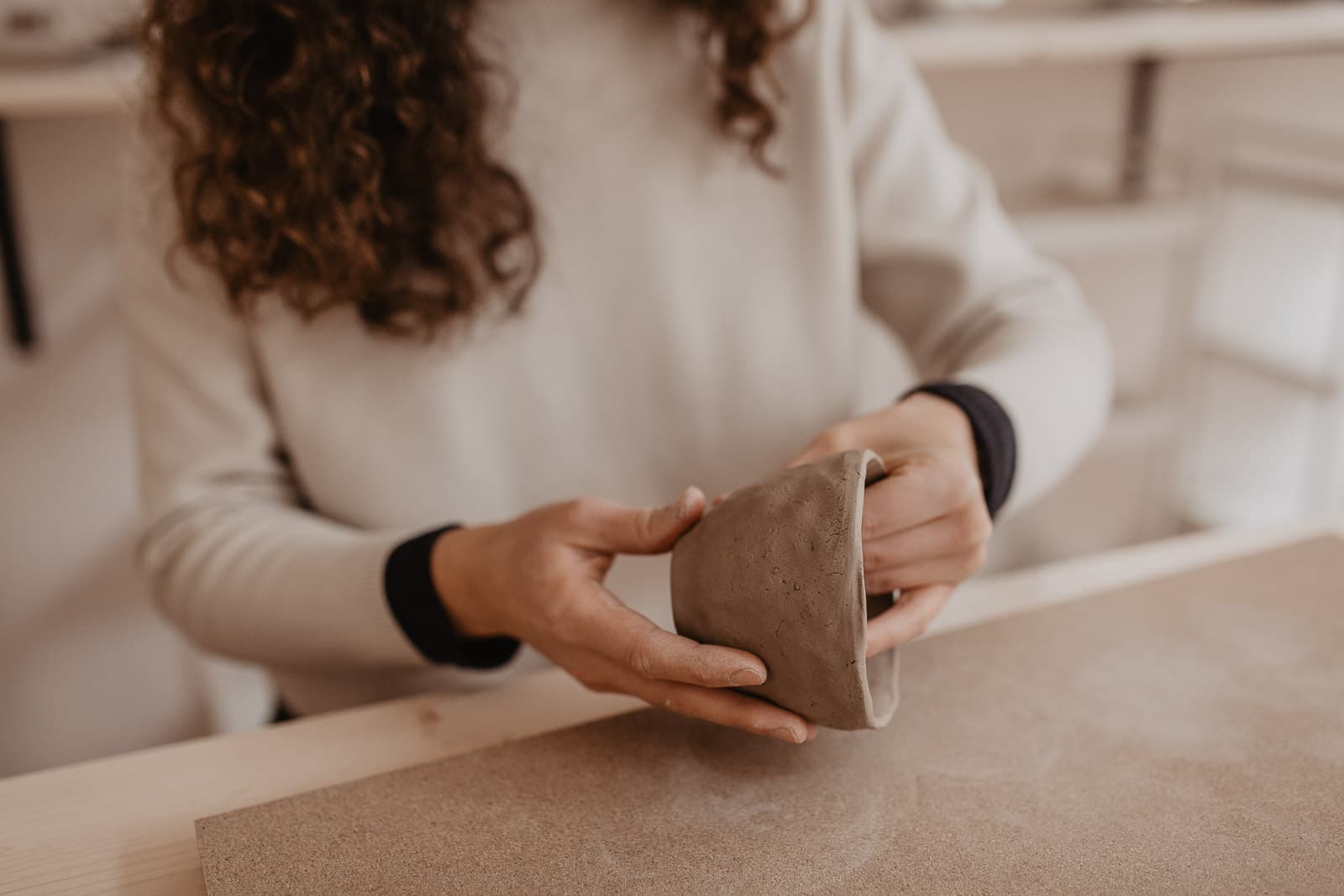
Choosing the right clay for your work
Choosing the right clay can be daunting. With this article, we wanted to give you a little prompter on how to evaluate the clay body that is best for you.
Though there are a lot of clays out there, they differ in a few aspects (we are simplifying a little for the sake of this article): composition (groggy or not groggy), state (liquid or plastic material), temperatures they can be fired at (low, medium or high temperatures). Clays also differ in chemical composition, water absorption rate and other technical features. However, if you are buying commercial clays, you likely have the following things to keep in mind.
The type of work you make (wheel, hand-building or slip casting)
If you throw on a wheel you are likely to choose a clay without grog. Grog is a ceramic material (rich in alumina and silica) that has been previously fired and ground down to small sand-like grains. There are a variety of grog types according to the size of the grain. Grog is usually added to clay to give it a texture, but also to reduce shrinkage and help with even drying (reducing cracks). It's therefore very helpful in hand-building, when you typically are making and attaching pieces in stages. While many use groggy clays to throw on the wheel too, it can be painful (literally) to use as it will cause abrasions on your hands.
If you slip cast, you are looking for a liquid clay. This is not just plain slip, however. Clay for slip casting has additional deflocculants which prevent the clay particles from sticking together and makes it into a pourable substance.
Temperature the kiln in your studio fires at
This is one of the most important aspects because it is the one that you likely have no control on, unless you have your own kiln. There are 3 types of clays:
1. Earthenware: clay bodies fired at lower temperatures (below 1200C). You may have encountered it in the form of terracotta. These clay bodies are not fired to a point of maturity (where they become completely dense). Their pores are not completely closed so they will let some water through unless glazed.
2. Stoneware: non-white clay bodies that are fired above 1200C. They are fired to maturity (if fired properly) and are typically very resistant and stable, ideal for every day use.
3. Porcelain: white clay body that is fired until 1400C. Porcelain has a beautiful translucent and delicate quality and is very strong.
Most community studios offer firings at cone 6 (1220C circa). We at Kleistone Studio offer firing services at cone 7 (1240C). This is a typical stoneware temperature and can also be used for some porcelains (though testing is required).
Wherever you get your clay fired, you should ensure that your commercial clay reaches maturity at or slightly below the temperature the kiln is firing at (usually designated on commercial clays as "mature at" or "dicht ab" in German), but also that its firing range is well within that temperature.
For instance, if you use a stoneware clay you and get it fired with us, you should ensure that it can be fired at least up to 1240C (or it will melt in the kiln).
End product you wish to produce: functional v sculptural
If you make functional work, we highly recommend stoneware clay because, if fired properly, it is strong and great for every day functional pieces such as mugs and plates. A piece's ability to sustain functional use is of course also dictated by the glaze and whether it's properly formulated, applied and fired, but this is a topic for another time.
Sculptural or decorative work on the other hand can benefit from earthenware because you often have access to brighter and more varied color palettes that would not be possible at higher temperatures.
You still need to test!
Finding the clay body for you can take a while. It's a good idea to try out a few clay bodies to understand how they differ in behaviour.
Different clays will have different shrinkage rates, which will also impact you if you make work that needs a certain degree of predictability.
We highly recommend to make test tiles to verify if they work well with your chosen glazes before producing work with a new clay.
Photo credit: Wild Lights Photography