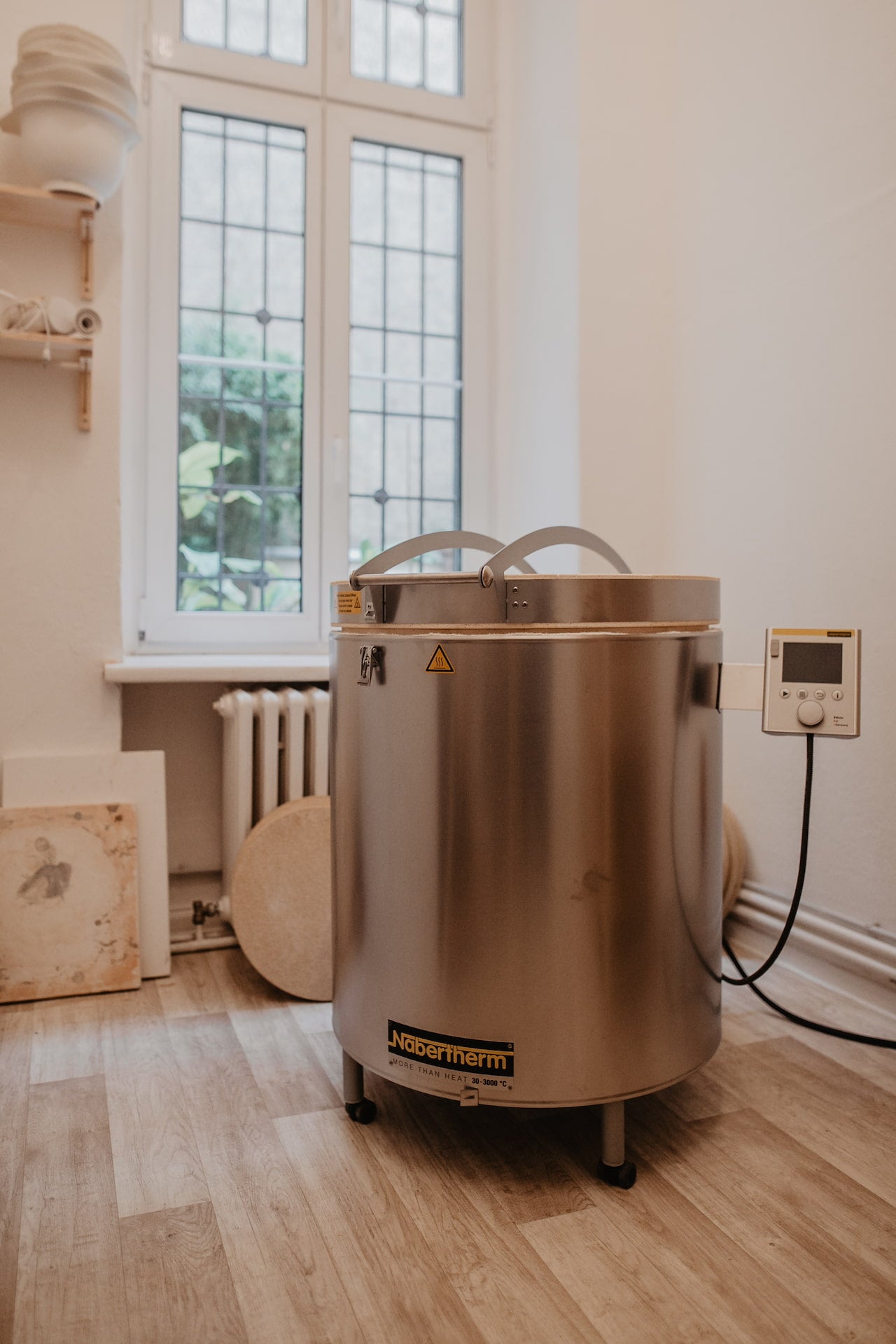
Thinking of getting a kiln? Things to keep in mind
While we wait for the arrival of our second kiln (name TBD), we thought of writing a little article about the things to keep in mind when deciding to get a kiln.
A kiln is a rather expensive piece of machinery, whose purpose is to reach and maintain the temperatures you need in order for your clay to vitrify and your glazes to melt. They are built with a thick layer of isolation (some are better than others at this) so that the heat stays inside the kiln. As a professional community ceramic studio, we have invested quite a bit of time in researching, procuring and maintaining our kilns. We also get quite a lot of questions about this aspect of our business, so below are some of the considerations to make if you are ever thinking of buying a kiln.
We will only be speaking about electric kilns in this article.
Front-loading v top-loading kiln
There are two types of electric kilns on the market: front-loading and top-loading. A front-loading kiln is loaded while standing. A top-loader (usually round-shaped, though square or octagonal also exist) is loaded from the top and you are required to reach down in the chamber to lower the work into it.
Front loaders are usually more expensive and demand more space. They tend to be more durable and, due to the fact that you can access them without reaching down, they are more efficient to load and demand less physical strain on your part.
Top loaders usually demand a little less space and are more affordable. Not all top loaders are created equal, however! See below for more information. Since we have been mostly using top-loaders, we will be discussing this type of kiln going forward.
Location
A kiln needs ventilation, either in the form of a vent or in the positioning of the kiln next to a window and in a well-ventilated place. Firing clay, especially in the beginning stages of a bisque fire, results in the burning off of organic materials and in the release of fumes, which need to be aired out. Our main kiln is standing next to a window, which we keep open any time the kiln is running (it always reaches temperature at night when we are not present). We also make sure to open all windows in the studio for better air circulation when we come back the next morning.
Furthermore, the kiln should be resting on a heat resistant surface and no objects should be placed in a 50cm radius around the kiln.
Can I operate a kiln in my home? We get this question very often and our answer is always: no, you should not operate a kiln in your home, unless you have a room that is separate from your living areas and very well ventilated. There are other considerations which speak against having a kiln at home, including (but not limited to) having the right electrical set up (see below) and having permission to operate your business from home (if you are running a business).
Electrical set-up
Not all kilns are created equal.
Broadly speaking, in Germany we have access to three types of electric kilns: kilns that run on a 2-phase electricity (240V - also called "Wechselstrom" in German, the "AC" in AC/DC), kilns that run on 3-phase electricity (400V - "Drehstrom" - also AC, not DC, that would be "Gleichstrom") and kilns that require a fixed connection to the electrical system. We will be focusing on the first two, as they are the most frequently purchased.
Here is where we need to take a small detour and talk about temperatures: kilns that run on 240V will typically be limited in the temperatures they can reach. If you are planning to work at cone 6 to 10 (stoneware to porcelain), you may be very limited in the brands and models that can safely reach those temperatures. They also typically are capped at 60L capacity for most brands, which will constrain the amount of work you can fire all at once.
These kilns may also be much less energy-efficient and their elements will require more frequent maintenance. You may be tempted to think that a 240V kiln can easily be placed in any household. To the contrary, you should always have a consult with an electrician, as these kilns will require a Schuko plug (the bulky continental European plug; Schuko is short for Schutzkontakt, "protective contact") and socket that runs at 16A. This means that the fuse behind the plug you want to use needs to be certified for 16A, which is not always the case, even in new buildings.
Kilns that run on 3-phase electricity (400V) require for the building and the specific unit to have it installed. Otherwise, it will necessitate the expensive retrofitting of the transformers in or near the building and in the unit. (This is what we had to do at our studio.) They also have their specific socket and plug: the CEE-Drehstromsteckverbinder (try saying that out loud quickly!).
These kilns, however, reach higher temperatures, can do so more quickly, are way more long-lasting and the physics suggest they will be significantly more efficient. They typically start at 80L capacity and go up to much larger volumes, which is ideal for studios.
Some 3-phase kilns will require 32A so always check the specs and book a consult with an electrician before making a purchase.
There is a difference in price between a 2-phase and a 3-phase kiln, but it's usually less stark when taking into account the longevity and efficiency of a 3-phase kiln.
Modern kilns usually provide accurate readings of how much each firing consumes, which will allow you to better price your work and gauge your costs.
Overall, there are plenty of considerations to make when purchasing a kiln. We hope this was a useful article!